Industrial Floor Coating
We provide industrial-grade epoxy flooring solutions that cater to your company's need for durable floors,
from surface preparation to floor coating application.
Surface Preparation
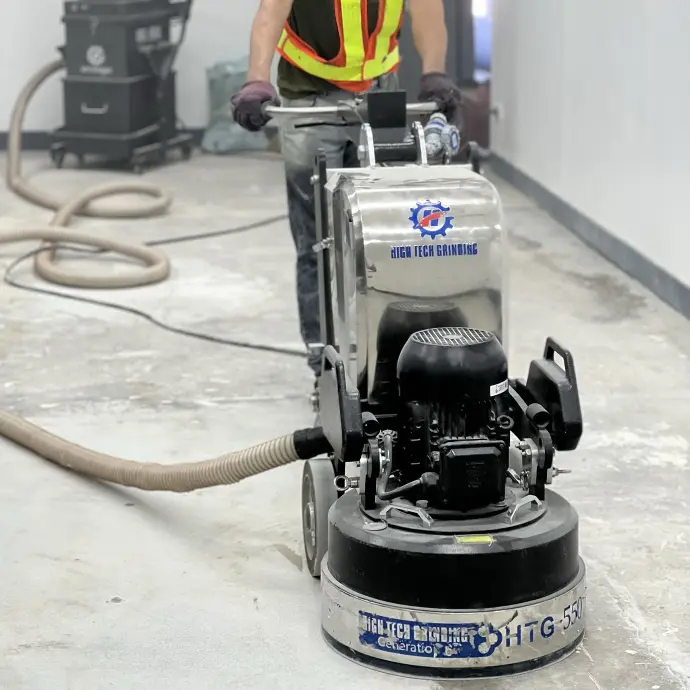
Mechanical Grinding
Involves removing the impurities in the cement mixture as well as the thin film of concrete for better adhesion.
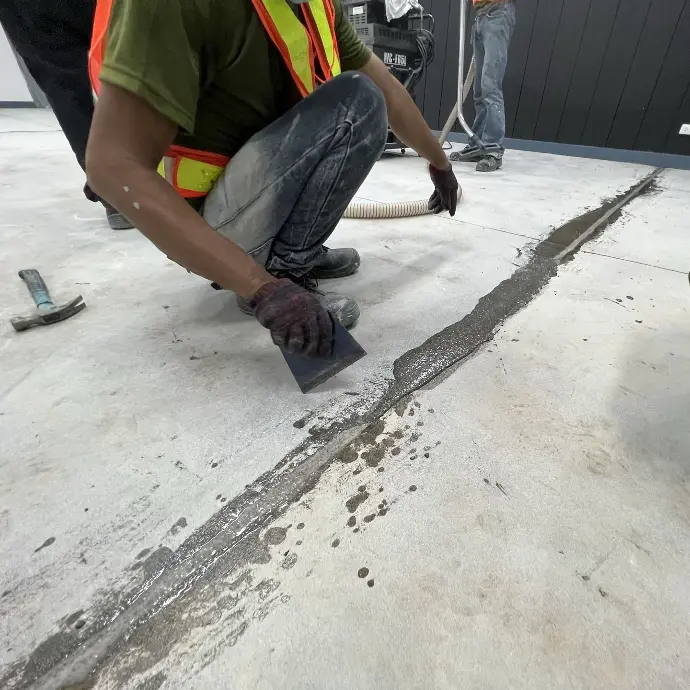
Concrete Repair
After grinding, epoxy grout and mortar is used for the patching and reparation of all major cracks that were identified.
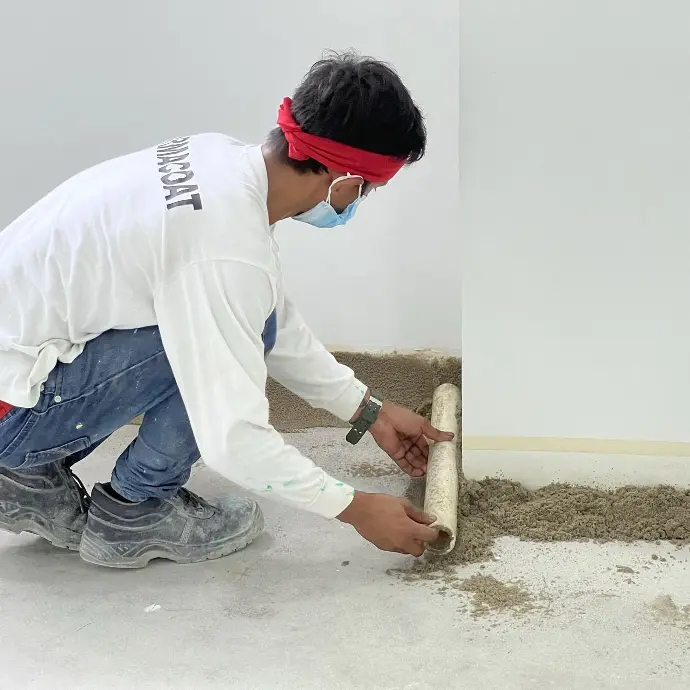
Coving Installation
Coving, or quarter C, is then installed to eliminate the corner between the floor and wall. This is typically required in high hygiene areas and clean rooms.
Before applying the epoxy flooring on the concrete surface, it first has to be surveyed for surface defects and other problems that could prevent the epoxy coat from adhering to the concrete properly. Concrete surface defects that are identified during surface preparation include blisters, dusting, delamination, cracks, low spots, spalling, and scaling & mortar flaking.
Surface preparation should eliminate these defects as well as other problems that were identified during the survey, if not it can pose a possible threat to the epoxy flooring's integrity in the long run.
Inadequate surface preparation is one of the most common mistakes made by applicators and it's important to get the process right because epoxy coatings need a clean and properly prepared surface to adhere well.
Done by Skilled Professionals.
Floor Coating Methodology
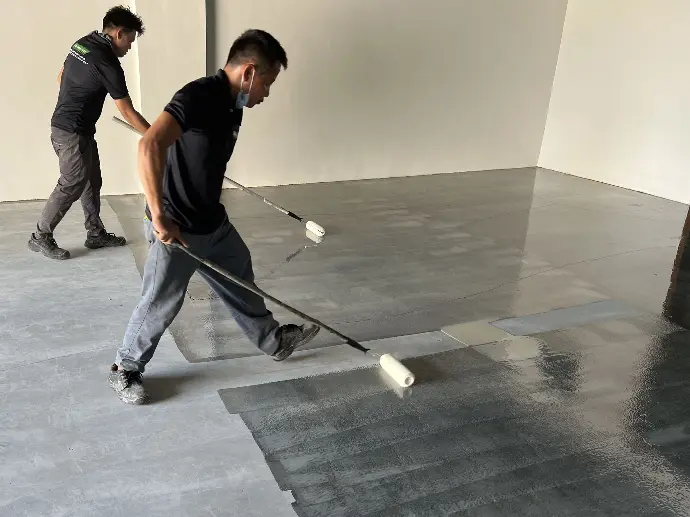
Primer & Sealer
The initial coating acts as both a sealer and a primer. The paint fills into the voids of the concrete that act as the water barrier.
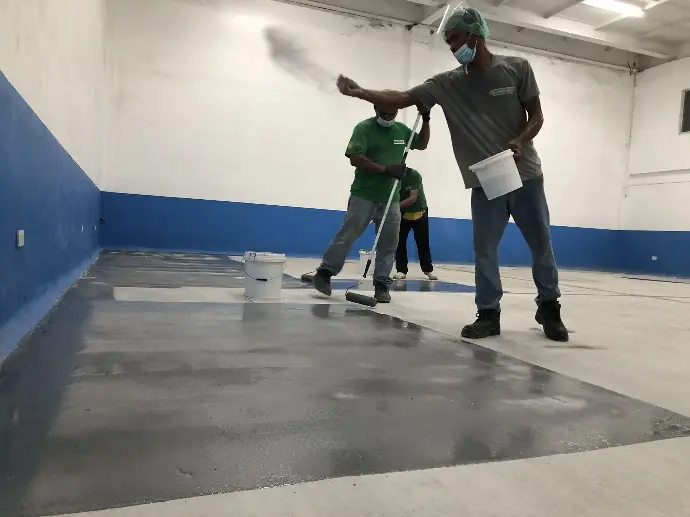
Silica broadcast
A layer of sand is broadcasted onto the primer as it dries. The layer helps in the build-up of paint, allowing the coating to achieve the desired thickness.
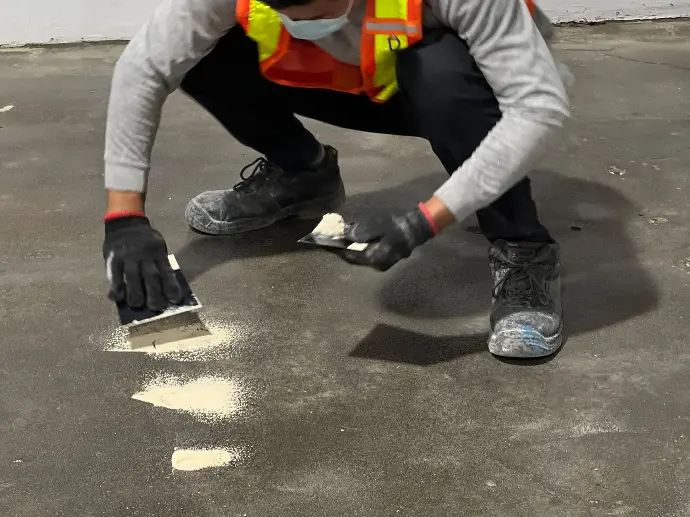
Surface Profiling
Surface profiling is done in between coatings. Cracks and crevices are patched using an epoxy putty.
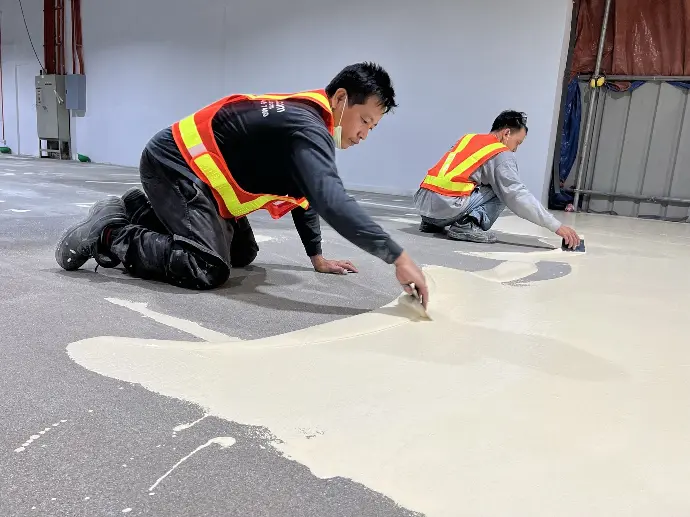
Intermediate Coat
Intermediate coat (mid-coat) is the second layer of paint and is applied either by a roller or as a putty. This coating is used as a base coat in the same color as the topcoat.
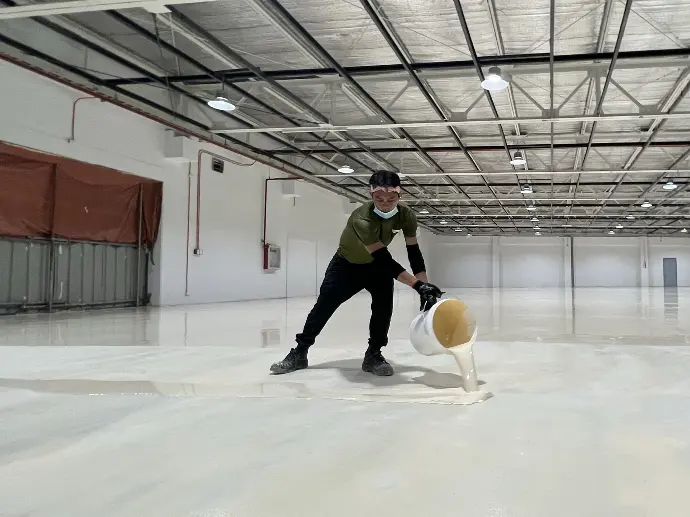
Self-leveling Topcoat
The upper most layer of of the painting process. The epoxy paint is poured and is spread using a roller at a rate of 1L-1.5L per square meter ensuring a seamless finish.
Application Process
To add a fourth column, reduce the size of these three columns using the right icon of each block. Then, duplicate one of the columns to create a new one as a copy.
It is important to determine which epoxy floor coating and which coat thickness is best suited for the area that will be worked on before the purchase and application of epoxy coats and related products. Ideally, it should be applied by an expert flooring solutions provider to ensure that no product is wasted and no mistakes are made during the application. This is because, besides the heavy equipment needed for surface preparation, epoxy products require their own set of special equipment, and have more specific procedures as well as curing times to follow before the ideal epoxy flooring is achieved.
We use industrial-grade tools and equipment to provide you with quality service and dependability. Our staff are professionally trained and Carmacoat can proudly claim that we have the knowledge, expertise, and experience—30 years worth!—needed to serve you.
30 Years of Experience.
Durability You Can Stand On
Request a quote or inquire about our services further by clicking the button below